Технологическое оборудование
Коррозия технологического оборудования является одной из важнейших проблем, с которой приходится сталкиваться при его эксплуатации. Коррозия зависит от многих факторов: от концентрации H2S и CO2, степени насыщения раствора, температуры, наличия абразивных примесей и т.д.
Основными агрессивными веществами являются кислые газы. Взаимодействие сероводорода со сталью приводит к образованию нерастворимого в растворе сернистого железа. Диоксид углерода в присутствии воды вступает в реакцию с железом с образованием бикарбоната железа, который при нагревании раствора переходит в нерастворимый карбонат железа, последний осаждается на стенках аппаратов и трубопроводов. Коррозия ускоряется в зоне парокапельной эрозии, на сварных швах.
Коррозии оборудования также способствует накопление в растворе твердых частиц, которые разрушают защитные пленки, вызывают эрозию металла. Такими твердыми частицами являются сульфид железа, окись железа, пыль, песок, прокатная окалина, которые попадают в колонны вместе с потоком нефтепродуктов.
Оборудование нефтегазоперерабатывающих установок помимо общей коррозии подвергается и другому виду разрушения — коррозионному растрескиванию. Зарегистрированы случаи появления коррозионных трещин в абсорберах, десорберах, теплообменниках, трубопроводах.
Вышеописанные факторы привели к тому, что в некоторых странах перешли на изготовление оборудования целиком из нержавеющей стали, несмотря на огромные первоначальные затраты. В России, как правило, основное оборудование установок очистки газа изготовляют из углеродистой стали и лишь наиболее подверженные коррозии узлы (трубные пучки теплообменников, кипятильников, холодильников) — из нержавеющей стали, скорость коррозии которой ниже, чем у углеродистой стали.
Из-за высокой стоимости нержавеющей стали изготовление из нее аппарата целиком экономически неэффективно. Широко известны стандартные методы продления ресурса аппаратов — изготовление их из углеродистой стали с припуском на коррозию, применение биметаллов. Однако каждое из этих решений имеет свои ограничения. Припуск на коррозию обуславливает существенно более высокий вес колонн, проблемы при доставке, монтаже. Биметаллические конструкции характеризуются повышенной сложностью при сборке, представляют повышенный риск в зоне сварных швов.
В 2003 году российская компания «Технологические Системы Защитных Покрытий» предложила новое решение для защиты внутренней поверхности колонн путем нанесения антикоррозионного износостойкого покрытия методом газотермического напыления. Для этого совместно с ВНИИГАЗ была проведена работа по определению коррозионной стойкости ряда материалов, нанесенных различными методами напыления. По результатам испытаний была выбрана высоколегированная нержавеющая сталь, нанесенная методом высокоскоростного газопламенного напыления (HVAF). Принцип работы установки основан на сжигании топлива в специальной камере сгорания с получением на выходе газовой струи, имеющей скорость до 2500 м/сек. Порошковый материал, подаваемый в газовый поток, разогревается и разгоняется до скоростей ~700…800 м/сек. Попадая на изделие, частицы порошка, обладающие высокой кинетической энергией, образуют плотное покрытие с высокими адгезионными характеристикам. Объемная доля воздуха в покрытии составляет не более 1%, а прочность сцепления с основой превышает 80МПа. Покрытие является многослойным, поэтому сквозная пористость отсутствует. Преимущество данного метода также заключается в том, что метод условно можно назвать «холодным», т.е. при нанесении покрытий не происходит нагрева деталей выше 120…150?С. Данный факт позволяет избежать каких-либо фазовых превращений в основном металле при нанесении покрытий.
В рамках контракта «ТСЗП» с «Газпром Добыча Астрахань» была разработана технология и изготовлен уникальный роботизированный комплекс для нанесения защитного покрытия методом высокоскоростного газотермического напыления внутренних поверхностей колонн без их демонтажа.
По результатам контроля за период более чем трехлетней эксплуатации колонн-абсорберов, отремонтированных методом газотермического напыления, был сделан вывод о прекращении процесса коррозионно-эрозионного износа, который составляет менее 0,1мм по сравнению с 8-10мм в год для колон без покрытия.
В процессе работы колонн регулярно проводятся наблюдения за поведением покрытия, и по результатам работы первых колонн была выявлена возможность развития подпленочной коррозии в нижней части колонны — в районе жидкой фазы. В связи с этим нами были проведены дополнительные исследования во ВНИИГАЗ, по результатам которых была предложена новая композиция, которая представляет собой двуслойное покрытие (табл.1) с подслоем менее склонным к развитию подпленочной коррозии. Применение двуслойного покрытия позволило увеличить межремонтный интервал покрытия с 3 до 5 лет.
Подслой ТСЗП-ВС-016.45 | Основное покрытие ТСЗП-ВС-013.45 | |
Химсостав покрытия | Fe Cr Ni B Si C | Fe Cr Ni Mo Si C |
Толщина | 100+20 мкм | 100+20 мкм |
Пористость | Менее 1% | Менее 1% |
Микротвердость | 650…800 HV | 500…570 HV |
Прочность сцепления | Более 70 МПа | Более 70 МПа |
Несмотря на то, что технология высокоскоростного газопламенного напыления обеспечивает получение покрытия без сквозной пористости, существует объемная пористость, которую желательно также закрывать. Для этой цели применяют различные пропитывающие составы на эпоксидной, акриловой или фторполимерной основе, имеющие низкую вязкость и высокую проникающую способность. Пропитывающий состав наносят после напыления всей поверхности кистью, валиком или распылителем.
На сегодняшний день данная технология защиты внутренней поверхности адсорберов включена как обязательная в регламент ежегодных планово-предупредительных ремонтов, произведено напыление всех колонн абсорберов, используемых в «Газпром Добыча Астрахань», на двух колоннах проведено ремонтное напыление.
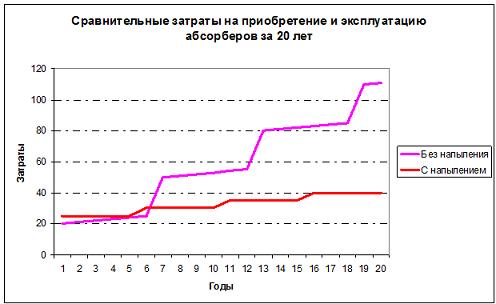
Экономический эффект заказчика составил несколько сотен миллионов рублей за четыре года работы. Эффект складывается из следующих факторов:
- Сокращение затрат на приобретение новых колонн (ранее колонна подлежала замене каждые 6 лет).
- Сокращение затрат на монтажные/демонтажные и пусконаладочные работы.
Технология и метод ее применения одобрены органами технического надзора России, имеются согласования от проектных организаций, положительные отзывы заказчиков. В настоящее время ведутся работы по исследованию применения наноструктурированных покрытий.
Сооружения
Для защиты сооружений от атмосферной и морской коррозии широко известны и в течение многих лет применяются за рубежом газотермические покрытия на основе цинка и алюминия. Применение таких покрытий разрешено ГОСТ 28302-89 «Покрытия газотермические защитные из цинка и алюминия металлических конструкций» и СНИП 2.03.11-85 «Защита строительных конструкций от коррозии».
Применение газотермически нанесенных металлических покрытий позволяет:
- Обеспечить покрытие крупногабаритных конструкций в сборе на месте;
- Существенно сократить затраты на регулярную покраску за счет резкого сокращения частоты покрасок;
- Повысить коррозионную стойкость конструкций за счет протекторного характера работы покрытий.
Несмотря на наличие необходимых регламентирующих документов и более чем 50-летний опыт успешного применения таких покрытий в США и Европе, в России факты применения газотермического напыления пока являются единичными. Так, с помощью алюминиевых и цинковых покрытий были защищены мосты третьего транспортного кольца и мост в Серебряном Бору в Москве, отдельные компании применяют данные технологии для защиты емкостей для хранения воды и нефтепродуктов, металлических дымовых труб, металлоконструкций.
Группа компаний «Технологические системы защитных покрытий» (ООО «ТСЗП») за 16 лет работы накопила огромный опыт восстановления, упрочнения, улучшения эксплуатационных и физико-механических характеристик рабочих поверхностей деталей машин и механизмов методами газотермического напыления и наплавки. Мы на постоянной основе сотрудничаем как со многими производителями оборудования, так и с заводами, использующими данное оборудование. Среди наших клиентов:
- ОАО «Газпромдобыча- Астрахань»
- ОАО «Аммофос»
- ОАО «Киришинефтеоргсинтез»
- ОАО «Салаватнефтеоргсинтез»
- ОАО «Салаватский машзавод»
- ОАО «Минеральные удобрения»
А.З. Лурье. Директор по развитию бизнеса ООО «Технологические системы защитных покрытий», В.В. Гераськин Исполнительный директор ООО «Технологические системы защитных покрытий».